MIT - Lathe
This lathe build was from the machine design class I took in undergrad. This was the class that gave me the most real-world mechanical engineering skills - we designed the system from scratch after doing a tear-down of a previous year’s lathe and we had to perform design reviews with the proper analysis to obtain our materials for every stage of build. I was the FEA lead of my group; we used ANSYS.
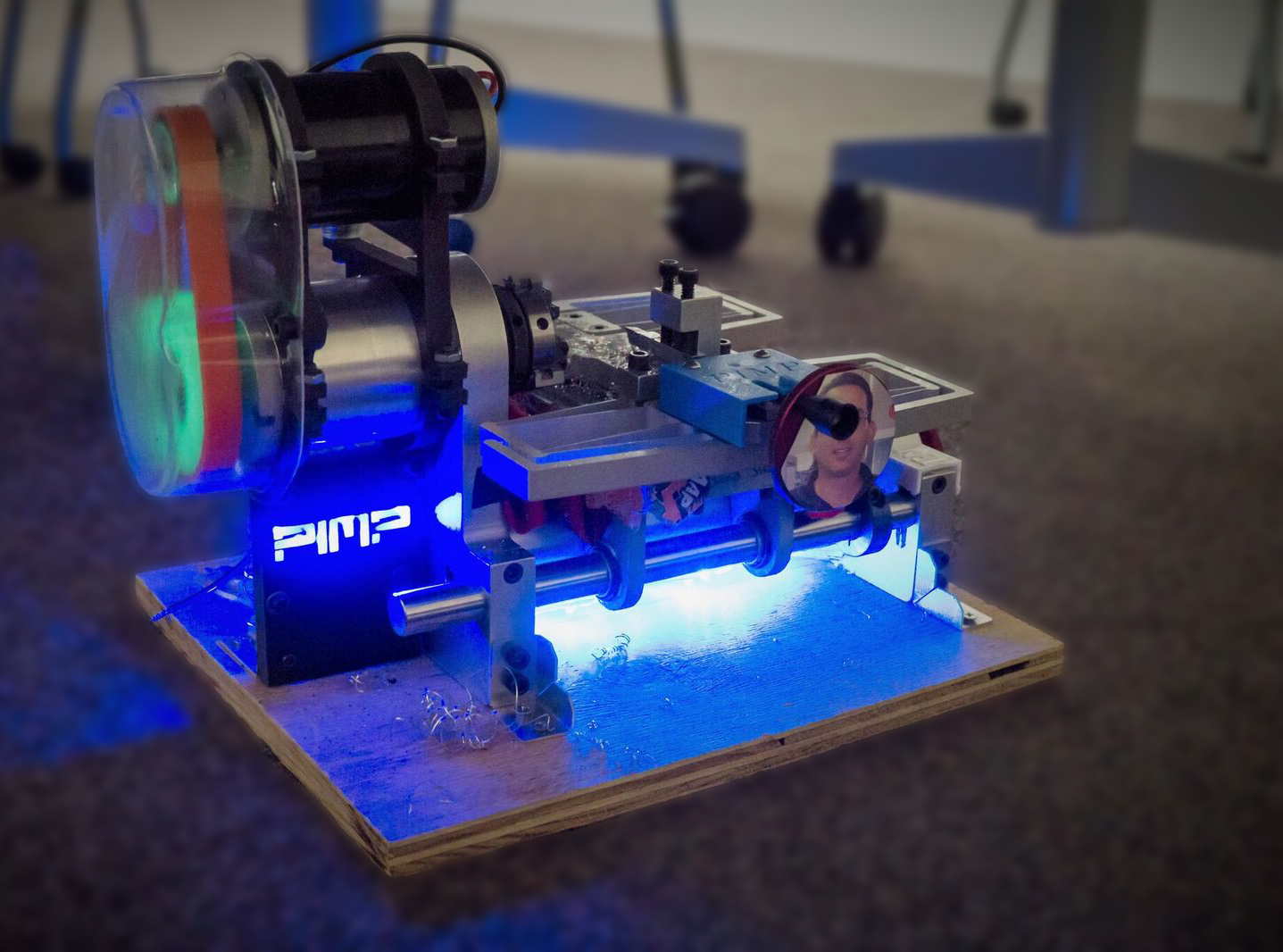
The three primary systems were the spindle, the “dancing man flexure”, and the crossfeed flexure. The spindle was made of steel and sat in an aluminum housing, and we had to ensure that the tapered roller bearings maintained preload regardless of temperature changes during machining.
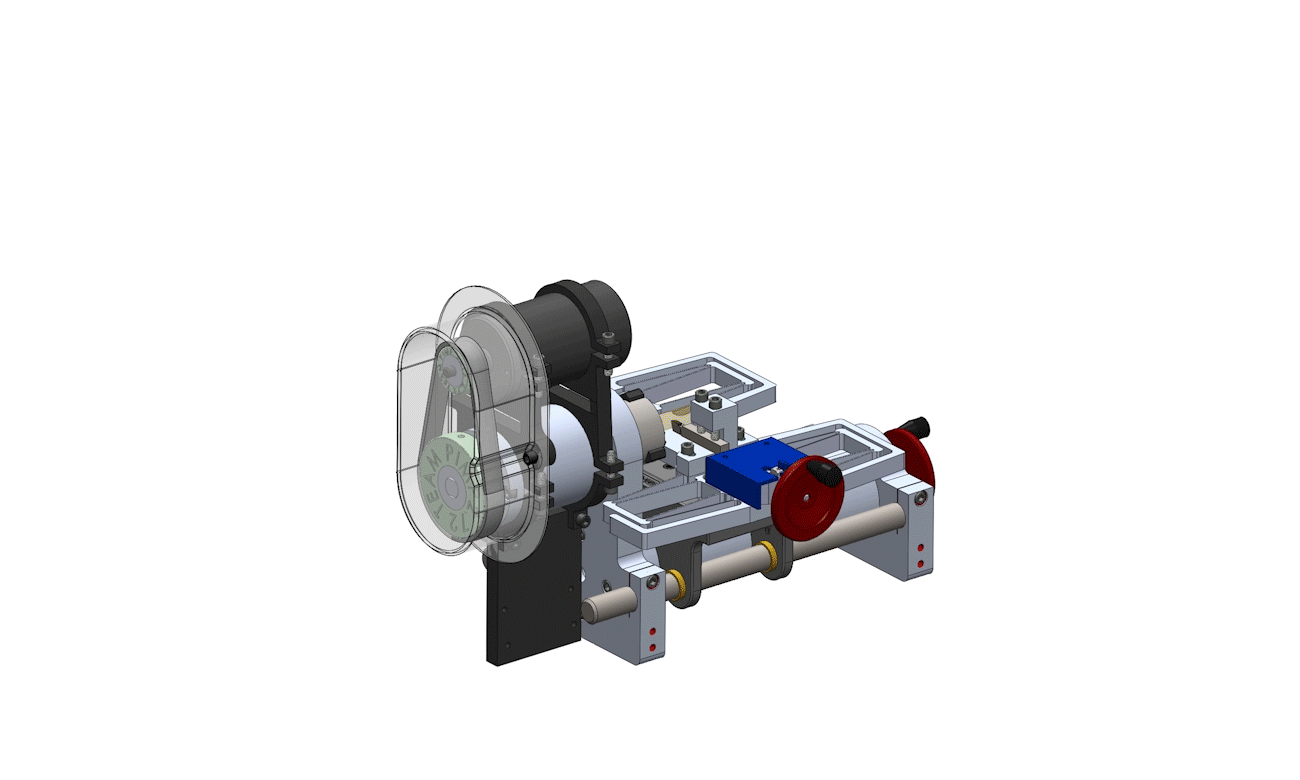
The crossfeed was a flexure that required lengthwise stiffness but transverse flexibility to move the cutting tool radially. The dancing man flexure connects the carriage to the lead screw nut; it also requires lengthwise stiffness but allows for misalignment between the lead screw and the carriage rails, which are cylindrical tubes that support the vertical load of the carriage (so that the lead screw is only responsible for translation of the carriage and does not lose efficiency due to friction under high loads).
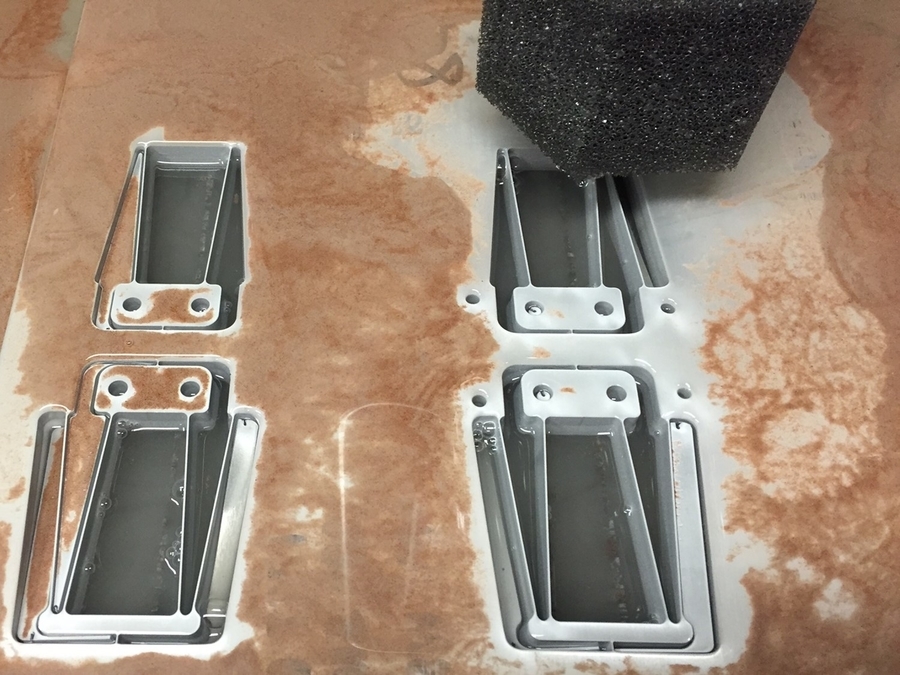
Finally, here’s a picture of our lathe doing the test cut – the passing condition of the class was to achieve 50 micron tolerance.
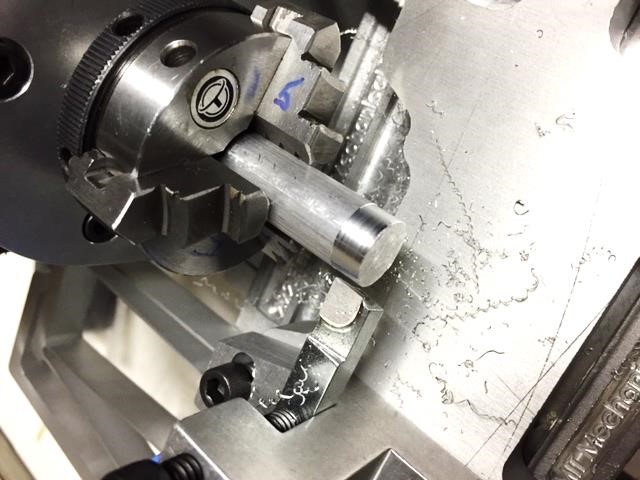
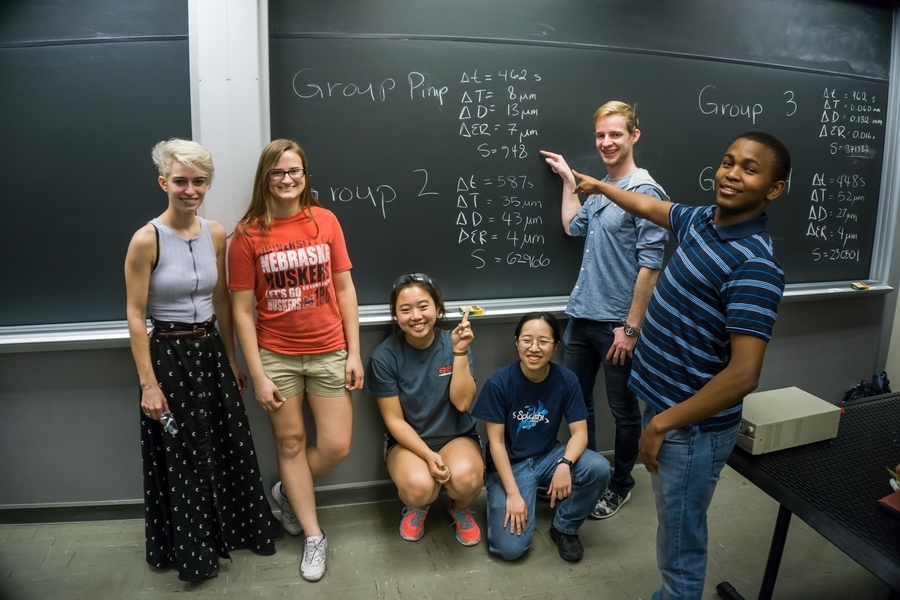